- Markets
- Catalogue
- Services and solutions
- Company
- Newsroom
- Tools & Resources
- Documents
- Nexans Insights
- Search
- Contact us
- Compare
- Sign in
Five innovations for buildings' revolution: Transforming buildings industry with 3D printing and modular construction
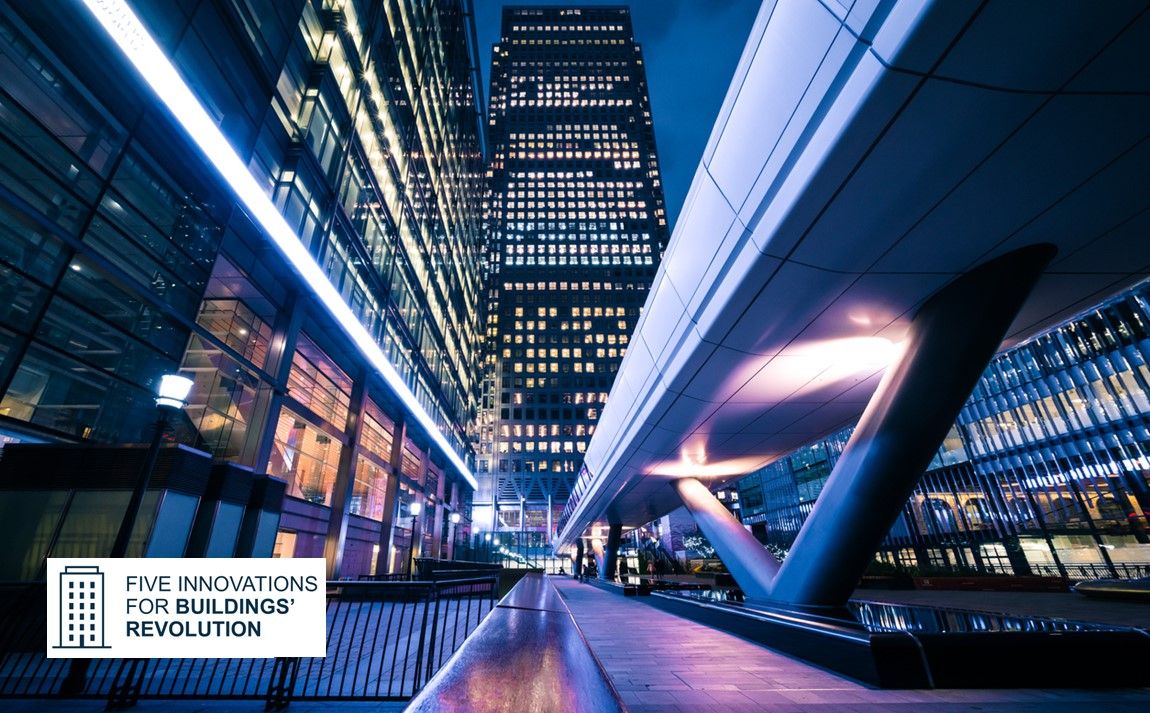
The building and construction industry is increasingly embracing newer technologies and solutions to meet rising floor space demand, stricter sustainability and safety standards, increasing costs, and skilled labor shortages.
As the demand for residential, commercial, industrial, and high-safety buildings is projected to grow in the coming years, meeting demand will require more efficient building construction methods. Those gaining in popularity are 3D printing, drones, robotics, and modular construction.
At the heart of this evolution in the building and construction industry is the increasing demand for electricity, which is expected to grow by 20% by 2030. This means future construction must take into account more electrical cables, connectors, systems, and subsystems, while ensuring smarter and safer installation and operations.
3D printing - from novelty to mainstream in reshaping buildings
Going from curiosity to a viable tool of the building trade, 3D printing, also known as additive manufacturing, is reshaping the industry and demonstrating its viability to dramatically reduce construction time and costs. Moreover, the benefits extend beyond on-site but to off-site (prefabrication) of building components, adding yet another major application and appeal to its uses.
One of the more progressive moves to 3D printing technology is the Dubai 3D Printing Strategy which aims for one-quarter of Dubai's buildings to be 3D printed by 2030. Examples include the 2,600-square-foot office complex housing the Dubai Future Foundation (DFF) headquarters and the Dubai Municipality completed by robotic construction company Apis Cor.
Benefits of 3D printing in construction have been highlighted during the 2023 Construction Technology ConFex:
- Speed and efficiency: The layer-by-layer additive manufacturing process of 3D printing can dramatically reduce construction time compared to conventional approaches, enabling the project to be completed more quickly.
- Reduced costs: By optimizing the use of materials and reducing labour requirements, 3D printing can reduce construction costs.
- Customization: 3D printing makes it possible to create custom designs and complex architectural elements that would be difficult to achieve using traditional construction methods. Complex and unique shapes can be easily created using 3D printing, allowing architects and designers to explore innovative design possibilities.
- Sustainable construction: Additive manufacturing can minimize material wastage by using only as much material as is needed, promoting sustainability in construction.
However, a number of challenges remain:
- Limits of scale and size: Scaling up 3D printing for large-scale buildings or infrastructure projects remains a challenge. Current technologies may not be able to efficiently produce structures beyond a certain size.
- Structural integrity and quality assurance: It is essential to guarantee the structural integrity and long-term durability of 3D printed components. Rigorous testing and quality assurance processes are required to meet safety standards.
- Integrating electrical systems and other services into 3D-printed structures requires careful planning and co-ordination to ensure their smooth operation.
- Regulatory and legal considerations: As 3D printing in construction becomes more widespread, regulatory frameworks and legal standards must be established to meet safety, liability and compliance requirements.
Robots and drones—redefining the building construction site
The construction robotic technology is going from sci-fi to reality in record-breaking time. A report from MarketsandMarkets expects the construction robots market to reach $166.4 million by 2023, representing a 16.8% compound annual growth rate (CAGR) from 2018 to 2023. And an IDC report published in January 2020 forecasts that demand for construction robots will grow about 25% annually through 2023.
Applications range from robots that can lay bricks and weld to self-driving diggers and drones that can survey and map construction sites and monitor progress. Most foresee robots assisting construction workers in repetitive and dangerous tasks while helping the industry tackle productivity and labor shortage challenges.
An example is Hilti’s semi-autonomous job site robot, Jaibot. Designed to assist mechanical, electrical, and plumbing (MEP) contractors, Jaibot uses BIM data to locate and drill holes for interior electrical and plumbing installations.
In the past couple of years, technologies not immediately embraced by the construction industry are now rightly finding their place, going from curiosity to a viable tool in the building trade.
Modular wiring—transforming the electrical landscape
With its roots dating back to the mid-'90s, Modular wiring revolutionizes the electrical landscape by replacing traditional installation methods with a convenient plug and play technology. It provides a quick, safe, and easy solution for connecting lighting and power circuits from the distribution board to the final connection point. Initially used in high-safety buildings like healthcare facilities, modular wiring is now widely utilized in schools and government buildings due to challenges such as labor shortages and increased infrastructure demands.
Over the past 30 years, modular wiring has gained popularity as a cost-effective and user-friendly alternative to traditional electrical installation. It offers numerous benefits throughout the entire construction process, from conception and design to operation and end-of-life. This has instilled confidence in governments, builders, and electrical contractors regarding its safety, cost-effectiveness, and efficiency for both new construction and upgrades.
To meet the increasing demand for floor space, architects and builders are relying more heavily on modular building techniques. According to a recent study by MarketsandMarkets, the global Modular Construction Market size is projected to grow from $91 billion in 2022 to $120.4 billion by 2027, up 5.7% from 2022 to 2027.
This trend is driven by the need for innovative approaches and the ongoing shortage of skilled labor. Modular wiring, along with other subassemblies and components, plays a vital role in enhancing productivity and performance while providing a comprehensive view of costs that includes factors like end-of-life, waste, and safety. With the construction industry shifting towards prefabrication and off-site construction, modular wiring will continue to grow in importance to meet government requirements, reduce costs, enhance quality and safety, and minimize environmental impact.
Wiring the future
Moving forward, the industry's biggest challenges are changing attitudes about adopting newer construction technologies and methods and more encompassing metrics.
This means that electrical cables are not seen as a commodity and, as such, not only selected on price but on type, materials, safety, and more. This changing of metrics sees performance, risk, and sustainability as essential criteria in the overall measurement of a building project.
In Oceania, Nexans supports its customers as they embark on the energy transition journey, offering a complete modular wiring solution. This solution is an efficient and sustainable way to minimize electrical site waste and reduce the cost of installation. Moreover, it encompasses switchboards, corridor wiring, and in-room wiring through to end-of-circuit accessories.
With building information management and design moving to more detailed phases earlier in the conception stage, the inclusion of modular wiring is gaining its place. In addition, supply concerns and rising material costs are increasingly driving electrical contractors to include modular wiring in bids and the design phase.
The future of modular wiring solutions is strong and will continue to gain in popularity due to the benefits of cost-savings, reliability, ease of installation, safety, quality, and sustainability.
Often regarded as a commodity industry, the construction sector is no exception to the trend towards new technologies and innovations. It has a multitude of tools and solutions that are revolutionizing not only processes, but also ways of working and preparing a site. Numerous innovations are already proving indispensable in improving the organization of worksites, the quality of work and the efficiency of teams. The result is a whole new way of designing projects and completing them in record time.
Sustainable development, improved worksite safety, technological solutions to save time and money, digital tools to build more environmentally-friendly structures... Innovation in the building industry is everywhere.
Our websites
Select your country to find our products and solutions
-
Africa
- Africa
- Ghana
- Ivory Coast
- Morocco
- North West Africa
- Americas
- Asia
- Europe
- Oceania